How to Avoid Mispicks in Your Warehouse
Online shopping is fun, but receiving the wrong item? Not so much..
Mispicks in the warehouse world might seem like small, isolated incidents, but they can have a massive ripple effect on your business. It leads to costly returns, extra shipping, and customer dissatisfaction. And that’s just the tip of the iceberg when it comes to the financial drain mispicks create.
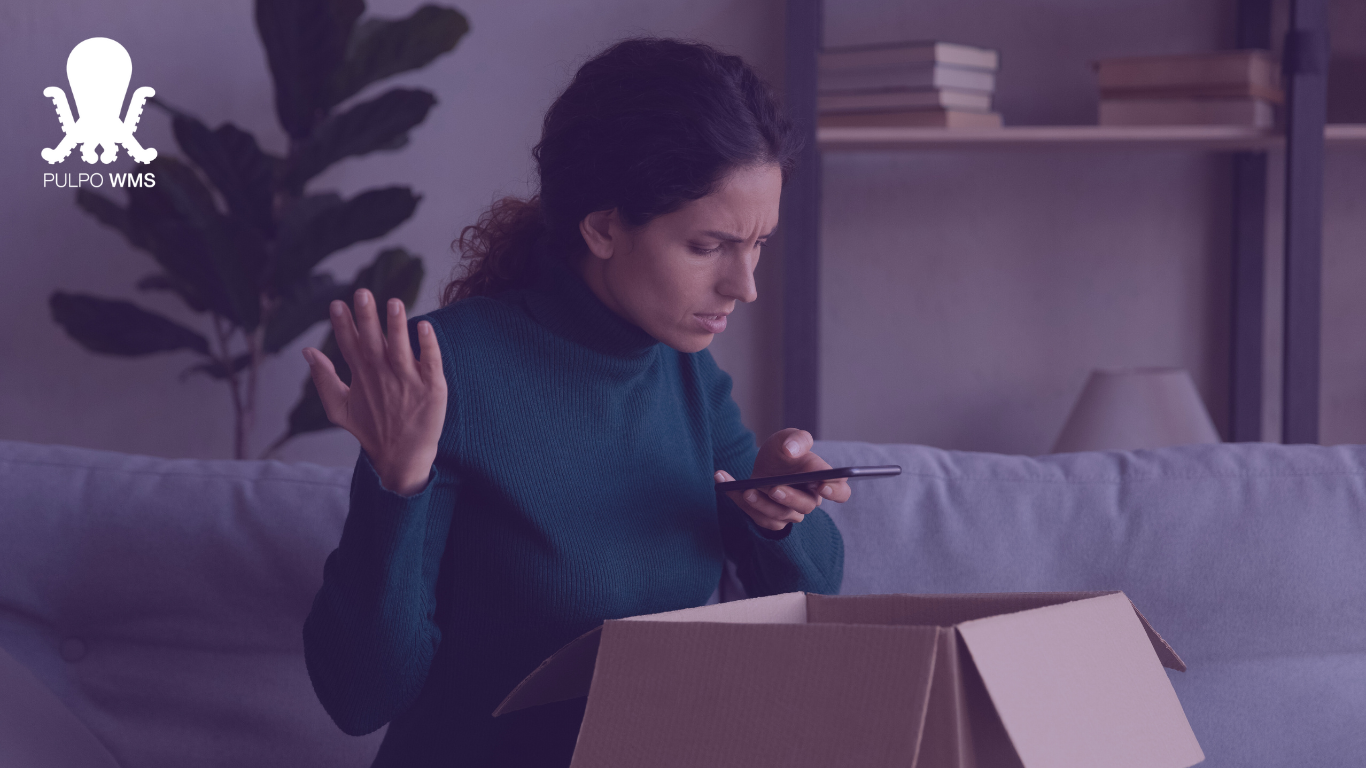
Why Do Mispicks Happen?
Human Error
Sometimes it's the result of employees rushing through their tasks, especially during peak seasons when order volumes are high. In other cases, inadequate training plays a major role—new or temporary staff may not have the familiarity needed to identify the correct products.
Incorrect Labeling
Without modern technology like automated barcode scanning or RFID systems, employees rely on inaccurate or unclear labels, leading to frequent mispicks. By not adopting advanced tech solutions, warehouses struggle with maintaining accuracy, slowing down operations and frustrating customers.
Manual Processes
Manual processes, by nature, leave room for errors. When employees rely on paper-based picking lists or outdated software, it’s easy for confusion to arise, and when it does, it’s your customer who ends up with the wrong item.
Hidden Cost of Mispicks
Imagine this: a customer eagerly places an order, excited to receive their package. But when it arrives, it’s the wrong item. Frustration sets in. Now, they must return it, wait even longer for the correct product, and wonder if they should have chosen a different company altogether. This small mistake snowballs behind the scenes, creating a cascade of costs for your business.
It’s not just the expense of sending out the right item that hurts. Industry reports reveal that the average warehouse loses nearly $400,000 a year due to mispicks. For businesses shipping globally or dealing with high-value products, that number only grows. While the cost of a single mispick, say $20, might seem manageable, these errors accumulate fast, eroding your profit margins bit by bit. But that’s just the surface.
Each mispick sets off a chain of inefficiencies—time wasted correcting the mistake, handling returns, and restocking products that shouldn’t have left in the first place. Meanwhile, your customer service team is spending valuable hours resolving complaints from frustrated buyers. These seemingly small hiccups end up diverting resources from what truly matters: getting the right orders out, on time, every time. It’s a financial sinkhole that silently pulls at every corner of your operation. Sounds familiar?
How PULPO WMS Can Help Reduce Mispicks
Automation is your best ally when it comes to eliminating manual errors. Implementing an advanced warehouse management system like PULPO WMS can significantly reduce mispicks. By automating the order picking process and incorporating real-time inventory tracking, you’re essentially taking human error out of the equation.
.png?width=2000&height=1125&name=Picking%20and%20Packing%20Screenshot%20(5).png)
Optimized and Structured Picking
- no paper involved
PULPO WMS significantly reduces human error by integrating advanced barcode scanning technology, ensuring that every item picked and packed is the right one. With PULPO’s pick and pack software, warehouse staff can work quickly and accurately, offering full traceability of each item throughout the entire fulfillment process. Our modern system eliminates manual data entry errors by instantly generating accurate shipping labels, which not only speeds up the process but also cuts down on costly mistakes.
Reduce Picking Errors to Net Zero
Handling higher order volumes? No problem. PULPO WMS is designed for seamless scalability with faster onboarding and minimal training required for new employees, ensuring that your team can hit the ground running. With features like zone picking and automated packing slip generation, PULPO's picking software optimizes every aspect of the order picking process, from the moment an item is picked to when it's shipped. This not only reduces mispicks but also increases overall efficiency, leading to faster fulfillment times and higher customer satisfaction.
.png?width=2000&height=1125&name=Picking%20and%20Packing%20Screenshot%20(7).png)
What makes PULPO WMS Unique
.png?width=200&height=128&name=Pulpo_Step1_Warehouse%20Wizard_01_2%20(1).png)
Picking Route Optimization
Our Warehouse Layout Configuration Tool, the Warehouse Wizard considers all possible paths to reach your warehousing positions and bins during the picking and packing process. Based on the items of your order it guides your employees without wasting time and with absolute order accuracy.
Multi-Order and Split Picking
Multi-order picking allows for the simultaneous collection of multiple orders, significantly reducing the time per pick and increasing overall throughput. With PULPO WMS Multi-order (Cluster) picking and batch picking are easily implemented, saving up to 70% of the time.

User Friendly Picking App
A Picking-App that is easy to use will shorten training times and increase productivity. Ensure it is compatible with affordable Android devices that provide barcode scanner integrations and better ergonomics. PULPO Warehouse management software helps reduce human error with integrated barcode scanning.
Book a Demo
Get a free customized warehouse optimization plan within our complete product tour encompassing:
- Logistic processes review
- Optimization analysis
- Cost optimization forecasting
- Processes integration with PULPO WMS
- Data centralization
- Integrations with your current software
Find out why PULPO WMS is regarded as the most modern Ecommerce WMS today!
Ready to boost your E-Commerce profitability?
Learn how PULPO WMS automates your logistics, enhances your warehouse management and optimize your operating costs, enabling your business to scale-up